A welding defect is any flaw that compromises the usefulness of a weldment. There is a great variety of welding defects. Welding imperfections are classified according to ISO 6520[1] while their acceptable limits are specified in ISO 5817 [2] and ISO 10042.[3]
Major causes[edit]
A lack of inter-run fusion which occurs between adjacent layers of weld metal on a multi-run welds; These are normally detected in welds where improper welding variables have been used and where there are improper manipulations of the electrode from the welding operator. Incorrect joint design and fit-up can also lead to lack of fusion issues. Lack of fusion is the result of the weld metal failing to fuse completely to the base metal or to the preceding weld bead. It’s caused primarily by improper welding gun angle or incorrect travel speed. Avoid this problem by maintaining a 0- to 15-degree gun angle during welding and keeping the arc on the leading edge of the weld pool. Pseudoarthrosis, which means lack of a solid fusion, is becoming a less common outcome of spinal fusion surgery thanks to modern instruments and surgical techniques. However, there are a number of fusion risks that can adversely create this outcome, including the patient's own health and personal habits (host factors) and the technique of the. Lack of fusion is a very dangerous weld defect in a welded structure. Because of the notch effect, a crack may further propagate under the smallest load applied. This type of defect is very difficult to detect with non-destructive testing methods. 2 ways to abbreviate Lack Of Fusion. How to abbreviate Lack Of Fusion? Get the most popular abbreviation for Lack Of Fusion updated in 2020.
According to the American Society of Mechanical Engineers (ASME), causes of welding defects can be broken down as follows: 41 percent poor process conditions, 32 percent operator error, 12 percent wrong technique, 10 percent incorrect consumables, and 5 percent bad weld grooves.[4]
Hydrogen embrittlement[edit]
Residual stresses[edit]
The magnitude of stress that can be formed from welding can be roughly calculated using:[5]
Where E is Young's modulus, α is the coefficient of thermal expansion, and ΔT is the temperature change. For steel this calculates out to be approximately 3.5 GPa (510,000 psi).
Types[edit]
Cracks[edit]
Defects related to fracture.
Arc strikes[edit]
An Arc Strike is a discontinuity resulting from an arc, consisting of any localized remelted metal, heat affected metal, or change in the surface profile of any metal object. [6]Arc Strikes result in localized base metal heating and very rapid cooling. When located outside the intended weld area, they may result on hardening or localized cracking, and may serve as potential sites for initiating fracture. In Statically Loaded Structures, arc strikes need not be removed, unless such removal is required in contract documents. However, in Cyclically Loaded Structures, arc strikes may result in stress concentrations that would be detrimental to the serviceability of such structures and should be ground smooth and visually inspected for cracks. [7]
Cold cracking[edit]
Residual stresses can reduce the strength of the base material, and can lead to catastrophic failure through cold cracking. Cold cracking is limited to steels and is associated with the formation of martensite as the weld cools. The cracking occurs in the heat-affected zone of the base material. To reduce the amount of distortion and residual stresses, the amount of heat input should be limited, and the welding sequence used should not be from one end directly to the other, but rather in segments.[8]
Cold cracking only occurs when all the following preconditions are met:[9]
- susceptible microstructure (e.g.martensite)
- hydrogen present in the microstructure (hydrogen embrittlement)
- service temperature environment (normal atmospheric pressure): -100 to +100 °F
- high restraint
Eliminating any one of these will eliminate this condition.
Crater crack[edit]
Crater cracks occur when a welding arc is broken, a crater will form if adequate molten metal is available to fill the arc cavity.[10]
Hat crack[edit]
Hat cracks get their name from the shape of the cross-section of the weld, because the weld flares out at the face of the weld. The crack starts at the fusion line and extends up through the weld. They are usually caused by too much voltage or not enough speed.[10]
Hot cracking[edit]
Hot cracking, also known as solidification cracking, can occur with all metals, and happens in the fusion zone of a weld. To diminish the probability of this type of cracking, excess material restraint should be avoided, and a proper filler material should be utilized.[8] Other causes include too high welding current, poor joint design that does not diffuse heat, impurities (such as sulfur and phosphorus), preheating, speed is too fast, and long arcs.[11]
Underbead crack[edit]
An underbead crack, also known as a heat-affected zone (HAZ) crack,[12] is a crack that forms a short distance away from the fusion line; it occurs in low alloy and high alloy steel. The exact causes of this type of crack are not completely understood, but it is known that dissolved hydrogen must be present. The other factor that affects this type of crack is internal stresses resulting from: unequal contraction between the base metal and the weld metal, restraint of the base metal, stresses from the formation of martensite, and stresses from the precipitation of hydrogen out of the metal.[13]
Longitudinal crack[edit]
Longitudinal cracks run along the length of a weld bead. There are three types: check cracks, root cracks, and full centerline cracks. Check cracks are visible from the surface and extend partially into the weld. They are usually caused by high shrinkage stresses, especially on final passes, or by a hot cracking mechanism. Root cracks start at the root and extent part way into the weld. They are the most common type of longitudinal crack because of the small size of the first weld bead. If this type of crack is not addressed then it will usually propagate into subsequent weld passes, which is how full cracks (a crack from the root to the surface) usually form.[10]
Reheat cracking[edit]
Reheat cracking is a type of cracking that occurs in HSLA steels, particularly chromium, molybdenum and vanadium steels, during postheating. The phenomenon has also been observed in austenitic stainless steels. It is caused by the poor creep ductility of the heat affected zone. Any existing defects or notches aggravate crack formation. Things that help prevent reheat cracking include heat treating first with a low temperature soak and then with a rapid heating to high temperatures, grinding or peening the weld toes, and using a two layer welding technique to refine the HAZ grain structure.[14][15]
Root and toe cracks[edit]
A root crack is the crack formed by the short bead at the root(of edge preparation) beginning of the welding, low current at the beginning and due to improper filler material used for welding. The major reason for these types of cracks is hydrogen embrittlement. These types of defects can be eliminated using high current at the starting and proper filler material. Toe crack occurs due to moisture content present in the welded area, it is a part of the surface crack so can be easily detected. Preheating and proper joint formation is a must for eliminating these types of defects.
Transverse crack[edit]
Transverse cracks are perpendicular to the direction of the weld. These are generally the result of longitudinal shrinkage stresses acting on weld metal of low ductility. Crater cracks occur in the crater when the welding arc is terminated prematurely. Crater cracks are normally shallow, hot cracks usually forming single or star cracks. These cracks usually start at a crater pipe and extend longitudinal in the crater. However, they may propagate into longitudinal weld cracks in the rest of the weld.
Distortion[edit]
Welding methods that involve the melting of metal at the site of the joint necessarily are prone to shrinkage as the heated metal cools. Shrinkage then introduces residual stresses and distortion. Distortion can pose a major problem, since the final product is not the desired shape. To alleviate certain types of distortion the workpieces can be offset so that after welding the product is the correct shape.[16] The following pictures describe various types of welding distortion:[17]
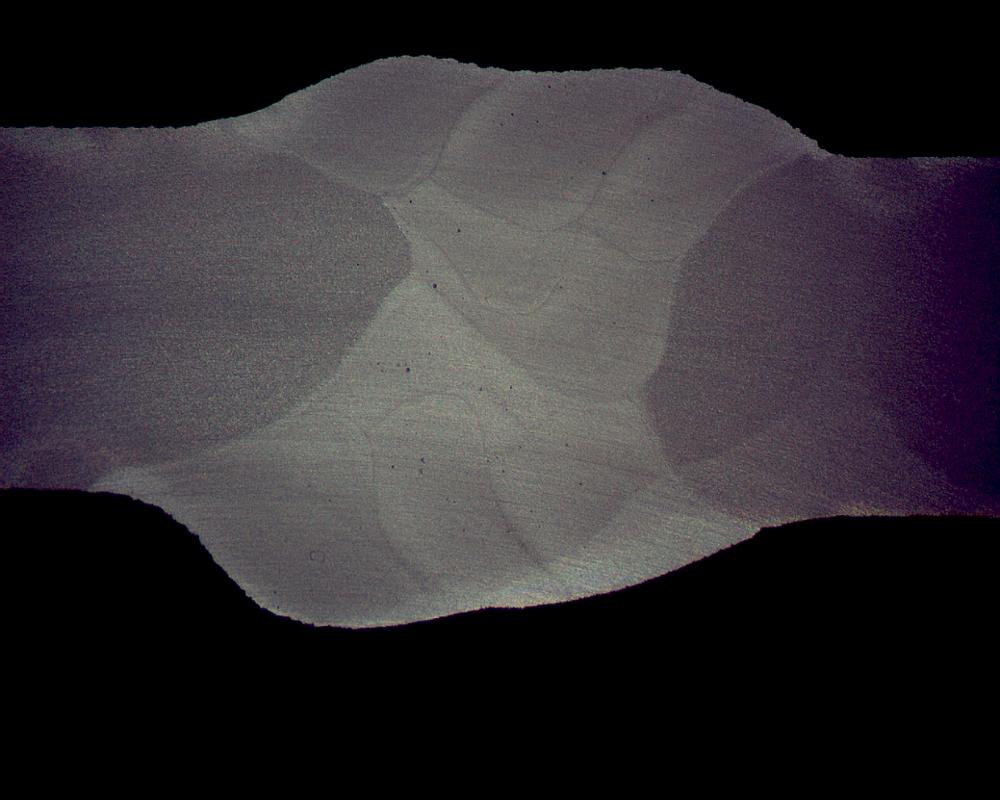
Lack Of Fusion Weld Defect
Transverse shrinkage
Angular distortion
Longitudinal shrinkage
Fillet distortion
Neutral axis distortion
Gas inclusion[edit]
Gas inclusions is a wide variety of defects that includes porosity, blow holes, and pipes (or wormholes). The underlying cause for gas inclusions is the entrapment of gas within the solidified weld. Gas formation can be from any of the following causes- high sulphur content in the workpiece or electrode, excessive moisture from the electrode or workpiece, too short of an arc, or wrong welding current or polarity.[12]
Inclusions[edit]
There are two types of inclusions: linear inclusions and rounded inclusions. Inclusions can be either isolated or cumulative. Linear inclusions occur when there is slag or flux in the weld. Slag forms from the use of a flux, which is why this type of defect usually occurs in welding processes that use flux, such as shielded metal arc welding, flux-cored arc welding, and submerged arc welding, but it can also occur in gas metal arc welding. This defect usually occurs in welds that require multiple passes and there is poor overlap between the welds. The poor overlap does not allow the slag from the previous weld to melt out and rise to the top of the new weld bead. It can also occur if the previous weld left an undercut or an uneven surface profile. To prevent slag inclusions the slag should be cleaned from the weld bead between passes via grinding, wire brushing, or chipping.[18]
Isolated inclusions occur when rust or mill scale is present on the base metal.[19]
Lack of fusion and incomplete penetration[edit]
Lack of fusion is the poor adhesion of the weld bead to the base metal; incomplete penetration is a weld bead that does not start at the root of the weld groove. Incomplete penetration forms channels and crevices in the root of the weld which can cause serious issues in pipes because corrosive substances can settle in these areas. These types of defects occur when the welding procedures are not adhered to; possible causes include the current setting, arc length, electrode angle, and electrode manipulation.[20] Defects can be varied and classified as critical or non critical. Porosity (bubbles) in the weld are usually acceptable to a certain degree. Slag inclusions, undercut, and cracks are usually unacceptable. Some porosity, cracks, and slag inclusions are visible and may not need further inspection to require their removal. Small defects such as these can be verified by Liquid Penetrant Testing (Dye check). Slag inclusions and cracks just below the surface can be discovered by Magnetic Particle Inspection. Deeper defects can be detected using the Radiographic (X-rays) and/or Ultrasound (sound waves) testing techniques.
Lamellar tearing[edit]
Lamellar tearing is a type of welding defect that occurs in rolledsteel plates that have been welded together due to shrinkage forces perpendicular to the faces of the plates.[21] Since the 1970s, changes in manufacturing practices limiting the amount of sulfur used have greatly reduced the incidence of this problem.[22]
Lamellar tearing is caused mainly by sulfurousinclusions in the material. Other causes include an excess of hydrogen in the alloy. This defect can be mitigated by keeping the amount of sulfur in the steel alloy below 0.005%.[22] Adding rare earth elements, zirconium, or calcium to the alloy to control the configuration of sulfur inclusions throughout the metal lattice can also mitigate the problem.[23]
Modifying the construction process to use casted or forged parts in place of welded parts can eliminate this problem, as Lamellar tearing only occurs in welded parts.[21]
Undercut[edit]
Undercutting is when the weld reduces the cross-sectional thickness of the base metal and which reduces the strength of the weld and workpieces. One reason for this type of defect is excessive current, causing the edges of the joint to melt and drain into the weld; this leaves a drain-like impression along the length of the weld. Another reason is if a poor technique is used that does not deposit enough filler metal along the edges of the weld. A third reason is using an incorrect filler metal, because it will create greater temperature gradients between the center of the weld and the edges. Other causes include too small of an electrode angle, a dampened electrode, excessive arc length, and slow speed.[24]
References[edit]
- ^BS EN ISO 6520-1: 'Welding and allied processes — Classification of geometric imperfections in metallic materials — Part 1: Fusion welding'(2007)
- ^BS EN ISO 5817: 'Welding — Fusion-welded joints in steel, nickel, titanium and their alloys (beam welding excluded) — Quality levels for imperfections' (2007)
- ^BS EN ISO 10042: 'Welding. Arc-welded joints in aluminium and its alloys. Quality levels for imperfections' (2005)
- ^Matthews, Clifford (2001), ASME engineer's data book, ASME Press, p. 211, ISBN978-0-7918-0155-0.
- ^Bull, Steve (2000-03-16), Magnitude of stresses generated, University of Newcastle upon Tyne, archived from the original on 2009-12-06, retrieved 2009-12-06.
- ^AWS A3.0: 2020 - Standard Welding Terms and Definitions
- ^aisc.org/steel-solutions-center/engineering-faqs/8.5.-repairs
- ^ abCary & Helzer 2005, pp. 404–405.
- ^[1] A Brief MIG welder Troubleshooting Guide
- ^ abcRaj, Jayakumar & Thavasimuthu 2002, p. 128.
- ^Bull, Steve (2000-03-16), Factors promoting hot cracking, University of Newcastle upon Tyne, archived from the original on 2009-12-06, retrieved 2009-12-06.
- ^ abRaj, Jayakumar & Thavasimuthu 2002, p. 126.
- ^Rampaul 2003, p. 208.
- ^Bull, Steve (2000-03-16), Reheat cracking, University of Newcastle upon Tyne, archived from the original on 2009-12-07, retrieved 2009-12-06.
- ^Bull, Steve (2000-03-16), Reheat cracking, University of Newcastle upon Tyne, archived from the original on 2009-12-07, retrieved 2009-12-06.
- ^Weman 2003, pp. 7–8.
- ^Bull, Steve (2000-03-16), Welding Faults and Defects, University of Newcastle upon Tyne, archived from the original on 2009-12-06, retrieved 2009-12-06.
- ^Defects/imperfections in welds - slag inclusions, archived from the original on 2009-12-06, retrieved 2009-12-05.
- ^Bull, Steve (2000-03-16), Welding Faults and Defects, University of Newcastle upon Tyne, archived from the original on 2009-12-05.
- ^Rampaul 2003, p. 216.
- ^ abBull, Steve (2000-03-16), Welding Faults and Defects, University of Newcastle upon Tyne, archived from the original on 2009-12-04.
- ^ abStill, J. R., Understanding Hydrogen Failures, retrieved 2009-12-03.
- ^Ginzburg, Vladimir B.; Ballas, Robert (2000), Flat rolling fundamentals, CRC Press, p. 142, ISBN978-0-8247-8894-0.
- ^Rampaul 2003, pp. 211–212.
Bibliography[edit]
- Cary, Howard B.; Helzer, Scott C. (2005), Modern Welding Technology, Upper Saddle River, New Jersey: Pearson Education, ISBN0-13-113029-3.
- Raj, Baldev; Jayakumar, T.; Thavasimuthu, M. (2002), Practical non-destructive testing (2nd ed.), Woodhead Publishing, ISBN978-1-85573-600-9.
- Rampaul, Hoobasar (2003), Pipe welding procedures (2nd ed.), Industrial Press, ISBN978-0-8311-3141-8.
- Moreno, Preto (2013), Welding Defects (1st ed.), Aracne, ISBN978-88-548-5854-1.
- Weman, Klas (2003), Welding processes handbook, New York, NY: CRC Press, ISBN0-8493-1773-8.
External links[edit]
Welding defects can be said to be the irregularities formed in a given weld metal as a result of incorrect welding patterns, wrong welding process, or due to poor welding skills from the welder’s part. Weld flaws may come in different sizes, shapes, and degrees of severity.
There are different types of welding defects that can transpire during the welding process. From porosity and cracking, to burn through and undercut, each has several causes.
However, regardless of the application and material on which they occur, one thing remains true to all of them; they’re common, costly, cause downtime and loss of productivity.
Luckily enough, there are various remedies that can help welders minimize these welding defects. In this article, we shall be discussing the seven most common welding defects, causes, and remedies plus 2 others.
Keep reading!
What are welding defects?
Welding defects/flaws can be defined as weld surface irregularities, imperfections, discontinuities, or inconsistencies that are formed in welded parts.
These defects differ from the desired weld bead size, shape, and quality. Welding defects could occur either from the outside or inside the weld metal.
Defects in weld joints could cause the rejection of parts and assemblies, an increase in the cost of maintenance, a reduction in performance and could cause catastrophic failures posing the risks of loss of life and property.
Welding defects and remedies
Mistakes sometimes occurs during a welding process. These could lead to different forms of welding defects. As a guide, We present to you the seven most common welding defects and their preventive measures.
1. Porosity
Lack Of Fusion Additive Manufacturing
Porosity usually occurs as a result of weld contamination. This happens when gas is trapped inside or along the surface of the weld metal. Just like other weld defects, Porosity results in weak welds that may easily collapse.
• Causes of Porosity:
Lack Of Fusion Porosity
Often, Contaminated or inadequate shielding gas is the common cause of porosity.
However, Porosity could also be caused by using too high gas flow, longer arc, inadequate electrode deoxidant, and the presence of paint, rust, grease, or oil.
At the same time, having a dirty base metal or extending the welding far beyond the nozzle could cause porosity.
Additionally, air currents from cooling fans may contaminate the shielding gas envelope around the weld-puddle, thereby causing porosity.
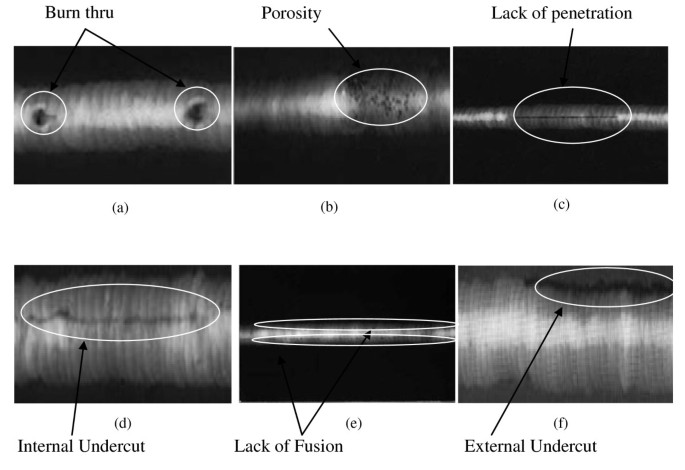
Another common cause of this welding flaw is poor seal (loose-fitting) in the shielding gas channel.
• Remedies for Porosity:
You can remedy the porosity of a weld by; cleaning the materials to be welded before you begin welding, using correct arc distance, employing the proper welding technique, and using the right electrodes.
Again, ensure that there is adequate gas flow and replace any gas hoses that may be causing leaks. Also, when welding outside or in drafty areas, place a welding screen around the work area. This will help ameliorate porosity issues.
2. Undercutting

Undercutting is a crater or groove that is formed near the toe of the weld. In this case, the weld metal fails to fill-in the grooved area resulting in a weak-weld that is liable to cracking along the toes.
• Causes of Undercutting:
Wrong filler metal, excessive heat, fast weld speed, as well as poor welding technique, may all leads to undercut welding defect on a welding joint.
Also, very high weld current, incorrect use of shielding gas and using the wrong electrode could cause undercuts.
• Remedies for Undercutting:
Undercutting in welding can be avoided by employing the right welding technique that does not involve excessive weaving.
Lowering the arc length and minimizing the travel speed of the electrode can also help prevent undercutting.
Another remedy to undercutting problem is adjusting the angle of the gun to point directly towards the weld joint.
3. Burn Through
As the name implies, burn through occurs when the weld metal penetrates through the base metal, burning through it. This kind of welding flaw is most common with soft or thin metals, especially those that are 1/4″ or less. Also too much weld penetration can often lead to burn through.
• Causes of burn through:
The primary cause of burn through is excessive heat. Also having too large root opening on the weld joint can results in burn through.
• Remedies for burn through:
When burn through occurs, the easiest way to rectify the problem is to lower the voltage and the wire feed speed.
Also increasing the travel pace can help remedy the problem, especially when welding on aluminum material.
Increasing the wire extension and using a weaving technique while welding can also help minimize the potential for burn through.
4. Incomplete Penetration
Incomplete joint penetration (lack of penetration) happens when there is a shallow fusion between the base metal and filler metal, rather than full penetration of the joint. It results in a gap, cracks, or even joint failure.
• Causes of incomplete joint penetration:
Incomplete joint penetration could occur when the groove you are welding is too narrow, and the weld metal does not reach the bottom of the joint.
Improper joint preparation and insufficient heat input are the two primary causes of lack of penetration. Improper shielding gas mixture and welding wire diameter can also be a factor.
Also, if you leave too much space between the two metals you are welding, the metals will not melt together on the first pass and hence results in incomplete penetration.
• Remedies for incomplete penetration:
There are a number of remedies for incomplete joint penetration; this includes; using higher wire feed speed and voltage, reducing the travel pace to allow more weld metal penetrates through the joint, and proper joint design and preparation.
The joint should be prepared in such a way to allow the welder to maintain the proper wire extension and still access the bottom of the weld joint. Again, ensure that ‘the wire type and diameters’ and ‘the gas and the gas mixture’ are compatible.
5. Cracks
Weld Cracks are the most serious type of welding defects. Weld Cracks are not acceptable in the welding industry.
However, a crack may occur just about everywhere in a weld; in the weld metal, on the plate next to the weld metal, or anyplace affected by intense heat.
The three major types of weld cracks are: Hot cracks, cold cracks, and crater cracks
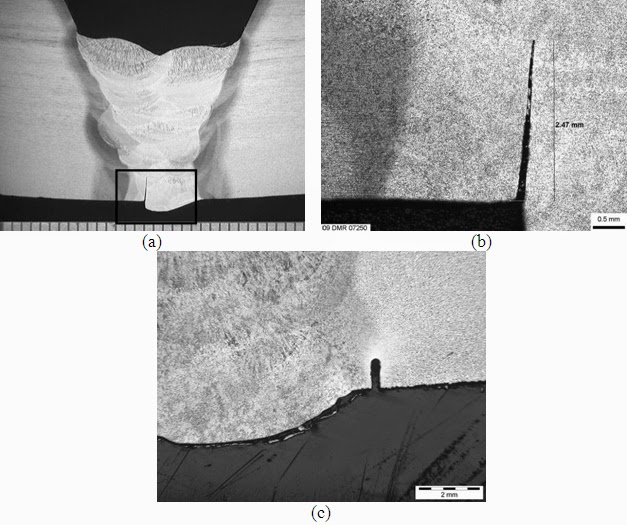
• Causes of weld cracks:
Weld Crack could be caused by so many things such as base metal contamination, poor joint design, failure to preheat before welding, low welding current, high welding speed, using hydrogen when welding ferrous materials and welding at too high voltage.
• Remedies for weld cracks:
You can prevent this type of weld flaw by using the right metal. Proper joint design and preparation is also another way to prevent cracking. Crater cracking can be prevented by using a backfilling technique. Right Selection of filler metal and shielding gas can also help prevent cracking problems.
6. Incomplete Fusion
Incomplete fusion occurs when the weld metal fails to properly fuse with the base metal, or when the individual weld beads don’t fuse together. This type of weld defect is also referred to as cold lap.
• Causes of incomplete fusion
Incorrect gun angle is the most common cause of incomplete fusion. However, contaminants on the base metal and insufficient heat can also cause this weld defect.
In some instances, too short arc length, very high travel speed, too low welding amperage or when the electrode size is too small for the thickness of the metal you are welding, all could result to incomplete fusion.
• Remedies for incomplete fusion:
The very first thing to do to prevent this weld flaw is to properly clean the base metal before you start the welding; make sure that the base metal is free of oil, grease, dirt or other debris.
Make sure the weld angle is between 0 to 15 degrees; this will allow you to fully access the groove of the weld.
Also, for joints that require weaving technique, holding the arc on the sidewall for some time is very vital to help prevent this type of defect. Ensure that there is enough heat input to coalesce the base metal and the weld metal fully.
7. Slag Inclusions
Slag is the waste material that is usually formed while welding, bits of this solid waste material may accidentally be incorporated into the weld and causes contamination.
• Causes of slag inclusions:
Some of the common causes of slag inclusions include failure to properly clean a welding pass before applying the next pass, incorrect welding angle, incorporation of flux from stick welding electrode, and too low welding amperage.
8. Warpage
Warpage is an unwanted distortion in the shape of a piece of metal. This occurs when the welder fails to properly control the expansion and contraction of the base material.
• Causes of warpage:

Warpage may arise when the welder clamps the welding joints too tightly, welding a piece of metal over and over again can also cause the metal to warp.
When welding a T-joint, the vertical part of the ‘T’ may sometimes pull itself towards the weld. Also, the more heat input you use, the more the chances you have to end up with a warpage.
• Remedies for warpage:
Warpage can be prevented by using only the required amount of heat. Opting for moderate travel speed and wire feed speed while welding can also help curtail the problem of warpage.
9. Overlap
overlap occurs when the weld face extends far above the weld toe. In this case, the weld metal rollout and forms an angle less than 90 degrees.
• Causes of Overlap
Overlap welding defect can arise when using large electrodes greater than the metal size. High welding current and the use of improper welding technique can also cause this defect.
• Remedies for Overlap
Overlap welding defect can be avoided by employing the correct welding Technique, using small Welding electrode and less welding has.
Conclusion
While welding defects and discontinuities may arise due to the welder’s poor welding skills, however, even the most skilled and experienced welders may in one way or another experience weld defects.
But the only way to stop these welding irregularities from negatively affecting productivity and increasing the cost of operations is by identifying and rectifying the problems as quickly as possible.